Carbon Steel Grades and Standards for Split & barred Tees
Carbon Steel Grades and Standards for Split & barred Tees – In this blog, we provide a comprehensive overview of the most commonly used carbon steel grades and standards for split tees and barred tees, focusing on their properties, applications, and industry demands. Whether you’re working in the oil & gas, petrochemical, or pipeline construction industries, this guide will help you understand which grades and standards are best suited for various conditions, such as high pressure, temperature variations, and corrosive environments. Learn how to select the right fittings to ensure safety, durability, and long-term performance in your pipeline systems.
Manufacturers of Carbon Steel Split & Barred Tees.
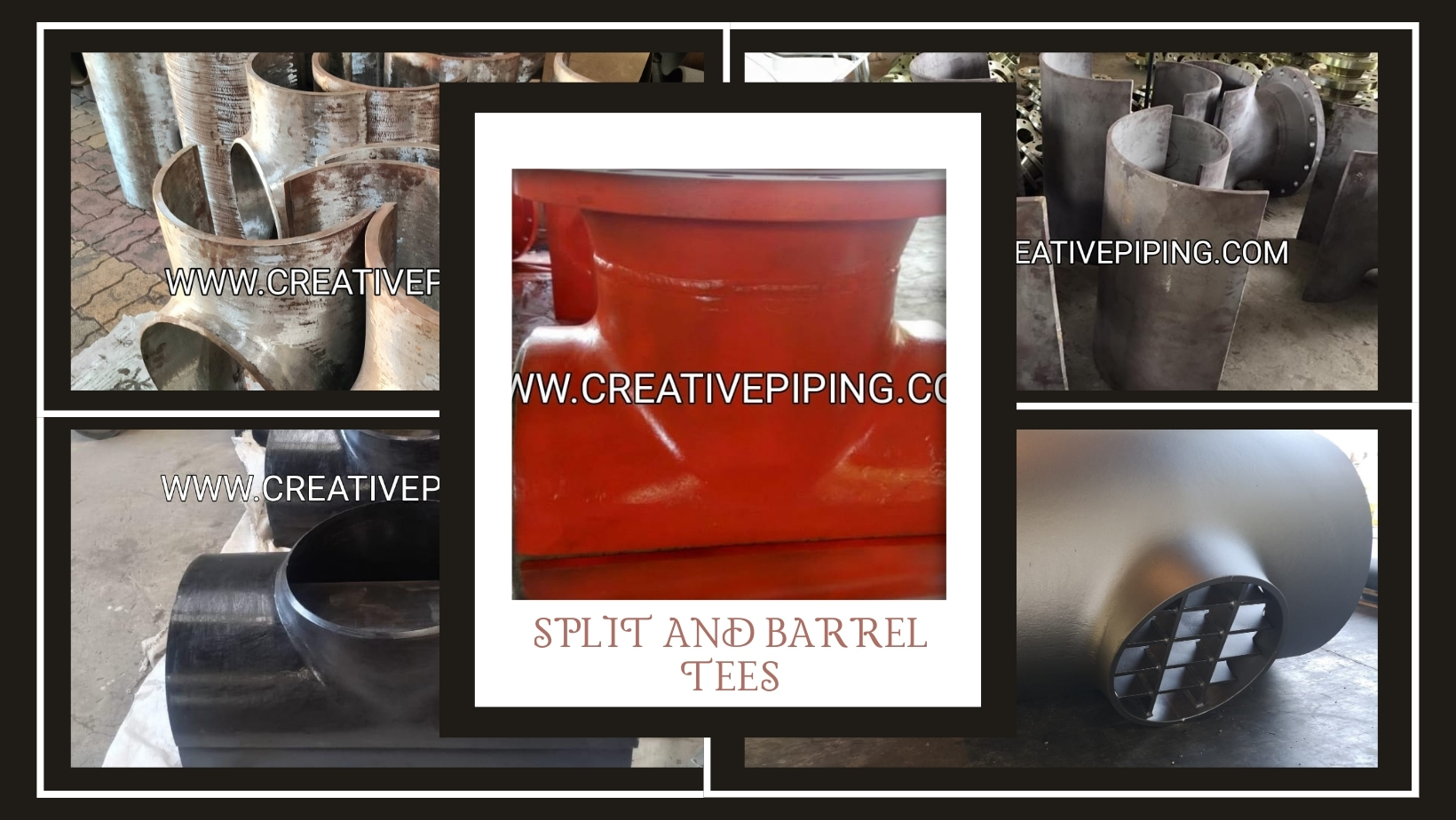
“Creative Piping Solutions”
Address: Ground Floor Shop No. 8/12, Plot No. 25/33, Ardeshirdadi Street, C. P. Tank, Girgaon, Mumbai-400004 Maharashtra, India.
Call/WhatsApp: +919079367689
Website: www.creativepiping.com
Email: sales@creativepiping.com
GST No.: 27KOEPS5029M1Z6
Split Tee:
A Split Tee is a specialized fitting used primarily in hot tapping operations. It consists of two halves (hence “split”) that are bolted or welded together around a pipe, allowing access for a branch connection without shutting down the pipeline.
Key Features:
- Application: Split tees are ideal for adding a branch connection (like a valve or another pipe) to an existing pipeline while it remains in service.
- Design: It has two pieces that enclose the pipeline, and a nozzle (branch) is welded onto the tee.
- Uses: It is widely used in the oil and gas industry for maintenance or modifications on live pipelines.
Barred Tee:
A Barred Tee is a specialized pipe fitting that includes internal bars or “baffles” inside the branch section of the tee to prevent pigging equipment from entering certain sections of a pipeline. The tee is used in piggable pipeline systems, where maintenance or inspection tools, known as pigs, are inserted into the pipeline for cleaning or inspection.
Key Features:
- Design: Barred tees have a standard tee structure but with bars welded inside the branch outlet to block the passage of pigs.
- Application: Primarily used in pipelines that require pigging operations, where it’s important to ensure that pigs do not enter certain branches of the pipeline.
- Uses: These tees are extensively used in the oil & gas and petrochemical industries to protect equipment during pigging operations and prevent unwanted flow diversions.
Types of Split Tees
Split tees and barred tees come in different types, depending on their design, usage, and specific pipeline requirements. Here’s an overview of the various types:
- Standard Split Tee:
- The most common type used in hot tapping operations.
- Designed to create a branch connection on an existing pipe without shutting down the system.
- Typically bolted or welded around the pipe.
- Welded Split Tee:
- Both halves are welded to the pipe instead of being bolted.
- Provides more permanent and stronger connections for high-pressure pipelines.
- Bolted Split Tee:
- Uses bolts to fasten the two halves together around the pipe.
- Easier to install and remove, making it ideal for maintenance tasks where disassembly might be required.
- Hot Tap Split Tee:
- Specifically designed for hot tapping, where modifications are made to live pipelines.
- The tee has provisions for connecting hot tap machines, ensuring safety and precision.
Types of Barred Tees
- Standard Barred Tee:
- The standard type with welded internal bars in the branch to prevent pigs from entering that section.
- Custom Barred Tee:
- Barred tees can be customized based on the specific needs of the pipeline system, such as the size and design of the internal bars or additional reinforcement for high-pressure systems.
- Flanged Barred Tee:
- These tees come with flanged ends for easy assembly and disassembly, often used where maintenance and frequent pigging operations are required.
Specialized Types (Common to Both Split and Barred Tees)
- Flanged Tee:
- Double Branch Tee:
- A tee that features two branch outlets instead of one, useful for systems that require branching in two directions from a single point.
These different types allow for flexible solutions depending on the pipe size, flow rate, pressure, and overall system requirements. They are essential for applications in the oil & gas, petrochemical, and industrial sectors.
What is Epoxy Coating?
Epoxy coating is a protective layer made from epoxy resin, a type of thermosetting polymer, often applied to metal surfaces to provide corrosion resistance, chemical protection, and improved durability. Epoxy coatings are widely used in various industries due to their excellent adhesion, toughness, and resistance to harsh environments.
Why We Use Epoxy Coating?
- Corrosion Resistance:
- Epoxy coatings protect metal surfaces, such as pipelines and fittings, from corrosion caused by exposure to moisture, chemicals, and other corrosive elements.
- Chemical Resistance:
- They offer excellent protection against chemical exposure, making them ideal for pipelines carrying corrosive substances, oils, and gases.
- Durability:
- Epoxy coatings create a hard, durable layer that resists wear and tear, mechanical damage, and impact, prolonging the life of the component.
- Abrasion Resistance:
- These coatings protect the metal from abrasion caused by particles and debris flowing through pipelines.
- Waterproofing:
- Epoxy coatings act as a barrier against moisture, preventing the underlying metal from rusting or degrading when exposed to water.
- Aesthetic Finish:
- Provides a smooth, shiny finish that enhances the appearance of metal parts and makes them easier to clean.
Is Epoxy Coating Used on Split Tees and Barred Tees?
Yes, epoxy coating is often applied to both split tees and barred tees to protect them from corrosion, wear, and chemical attack, particularly in aggressive environments.
Conditions Where Epoxy Coating is Used on These Tees:
- Underground Pipelines:
- Split and barred tees used in buried pipelines are often coated with epoxy to protect against moisture, soil chemicals, and corrosion over time.
- Offshore or Subsea Applications:
- In the oil & gas industry, subsea pipelines and fittings, such as split and barred tees, require epoxy coatings to resist saltwater corrosion and marine growth.
- High-Corrosion Environments:
- When these tees are used in environments with corrosive fluids (e.g., chemicals, acids, seawater), epoxy coatings prevent metal degradation.
- Water Supply and Wastewater Systems:
- In water distribution systems, epoxy coatings are applied to prevent rust and protect against contaminants that could affect water quality.
- High-Temperature Operations:
- Epoxy coatings that are heat-resistant can be applied to tees used in high-temperature environments where corrosion risks increase due to heat exposure.
- Aggressive Fluid Handling:
- For tees used in pipelines transporting harsh chemicals (e.g., acids, solvents, or gases), epoxy coatings help ensure the integrity of the fittings and prevent chemical attack on the metal.
Benefits of Epoxy Coating on Tees:
- Extended Lifespan: Protects tees from environmental and operational wear, significantly extending their service life.
- Reduced Maintenance: Lower risk of corrosion or mechanical damage means fewer repairs and less frequent maintenance.
- Improved Safety: Reduces the risk of pipeline failure due to corrosion or wear, which can lead to leaks, spills, or hazardous situations.
Carbon Steel Grades and Standards for Split Tees and Barred Tees
Carbon steel is a widely used material for split tees and barred tees due to its strength, durability, and cost-effectiveness. The specific grades and standards for these tees depend on their application, pressure requirements, and environmental conditions. Below are the most commonly used carbon steel grades and standards, which are also in high demand:
Carbon Steel Grades
ASTM A234 WPB
- Description: The most commonly used grade for butt-weld fittings, including tees.
- Properties:
- Suitable for moderate- and high-temperature applications.
- Good mechanical properties, including tensile strength and hardness.
- Applications: Widely used in oil & gas, petrochemical, and power generation industries.
ASTM A105
- Description: This is a specification for forged carbon steel fittings.
- Properties:
- Used primarily for flanges, valves, and fittings in high-pressure and high-temperature applications.
- Offers excellent machinability and weldability.
- Applications: High-demand in industries like oil refineries, chemical plants, and pipelines.
ASTM A350 LF2
- Description: A low-temperature carbon steel grade, suitable for fittings that require toughness at lower temperatures.
- Properties:
- Excellent impact resistance at low temperatures.
- Good weldability and mechanical strength.
- Applications: Used in cold climate conditions, such as arctic regions, for oil & gas pipelines and refineries.
ASTM A516 Grade 70
- Description: This grade is commonly used for pressure vessels and piping components.
- Properties:
- High tensile strength and excellent notch toughness.
- Ideal for use in lower-temperature and high-pressure environments.
- Applications: Mostly used in pressure vessels, boilers, and piping systems where high-pressure applications are involved.
ASTM A333 Grade 6
- Description: Low-temperature carbon steel pipe fittings, ideal for sub-zero conditions.
- Properties:
- Provides excellent performance in cold temperatures, especially for cryogenic piping systems.
- High toughness and impact resistance.
- Applications: Used in cryogenic pipelines and low-temperature refinery processes.
EN 10253-2 Grade P265GH
- Description: This is a European standard steel grade, equivalent to ASTM A234 WPB.
- Properties:
- Suitable for high-pressure piping systems.
- Offers good toughness and weldability.
- Applications: Used in steam boilers, pressure vessels, and chemical processing plants.
API 5L Gr. B / X42 / X52
- Description: Commonly used for line pipes in the oil & gas industry.
- Properties:
- X42 and X52 have higher yield strengths compared to standard Gr. B.
- Excellent corrosion resistance and toughness.
- Applications: High-demand in pipeline systems for oil and gas transmission, both onshore and offshore.
Standards for Carbon Steel Tees
These fittings are manufactured according to a range of international standards to ensure quality, safety, and compatibility with different industrial systems:
ASME B16.9
- Scope: Covers factory-made wrought steel butt-welding fittings, including split tees and barred tees.
- Key Focus: Ensures that the fittings meet certain dimensional and material requirements for use in high-pressure systems.
- Applications: Used extensively in petrochemical plants, refineries, power plants, and oil & gas pipelines.
MSS SP-75
- Scope: Specifications for high-strength, wrought, butt-weld fittings.
- Key Focus: This standard applies to tees used in pipeline systems with high-pressure and critical service conditions.
- Applications: Ideal for pipeline systems in the oil & gas industry, especially for transporting high-pressure fluids.
DIN 2615
- Scope: German standard for seamless and welded tees used in piping systems.
- Key Focus: Focuses on the quality and performance of carbon steel fittings.
- Applications: Commonly used in European and international markets, especially in pressure vessels, chemical plants, and pipelines.
EN 10253-2
- Scope: European standard for butt-welding fittings, including carbon steel split and barred tees.
- Key Focus: Applies to steel grades used in high-pressure systems.
- Applications: Common in chemical and refinery plants, particularly in Europe.
Carbon Steel Tees in High Demand
The demand for specific carbon steel grades and standards depends on various factors, such as the industry, operating environment, and application requirements. Here are some common applications and the most in-demand grades for these industries:
- Oil & Gas Industry:
- ASTM A234 WPB, ASTM A105, API 5L X42/X52 grades are highly in demand for high-pressure pipelines and onshore/offshore drilling systems.
- Petrochemical Plants:
- ASTM A234 WPB and ASTM A350 LF2 are frequently used for both high- and low-temperature operations, especially in corrosive environments.
- Power Generation:
- Carbon steel grades such as ASTM A516 Grade 70 and ASTM A234 WPB are used for pressure vessels and boiler systems.
- Cryogenic Applications:
- ASTM A333 Grade 6 is in high demand for low-temperature pipelines transporting natural gas or other fluids at sub-zero temperatures.
- Chemical Processing:
- Standards such as EN 10253-2 P265GH and DIN 2615 are commonly applied in chemical and refinery plants for handling high-pressure and corrosive fluids.
Summary:
The choice of carbon steel grades and standards for split tees and barred tees is critical for ensuring the safety, durability, and performance of the piping system. High-demand grades like ASTM A234 WPB, ASTM A105, ASTM A516 Grade 70 are preferred for their strength, corrosion resistance, and adaptability in high-pressure and high-temperature environments across industries such as oil & gas, petrochemicals, and power generation.
Follow us on Medium